Manufacturing of Pressure vessel:
What is Pressure Vessel?
Pressure vessels are enclosed containers used to hold liquids, vapors, and gases at a pressure significantly higher or lower than the ambient pressure. They are widely used in various industries such as petrochemical, oil and gas, chemical, and food processing industries. Equipment such as reactors, flash drums, separators, and heat exchangers are examples of pressure vessels.
Each pressure vessel must be operated within its design temperature and pressure, which is the pressure vessel‘s safety limits. The design, construction, and testing of pressure vessels are extensively carried out by knowledgeable personnel and are governed by regulations because the accidental release and leakage of its contents is a danger to its surrounding environment. Some of the well-known standards are the American Society of Mechanical Engineers Boiler and Pressure Vessel Code (ASME BPVC) Section VIII, and the American Petroleum Industry (API) 510 Pressure Vessel Inspection Code.
Types of Pressure Vessel according to their purpose
Storage Vessels are used to hold liquids and gases for industrial purposes. The vessel may be used to contain fluids in a later process, or for storing finished products such as compressed natural gas (CNG) and liquid nitrogen. Carbon steel is the most commonly used material for storage tanks.
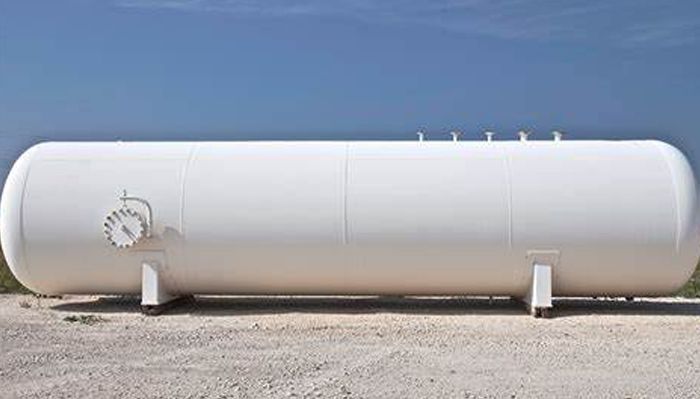
Heat Exchangers are used to transfer heat between two or more fluids. They are commonly used in the food, pharmaceutical, energy, and bioprocessing industries. The operation of heat exchanger equipment depends on the thermal and flow properties of the fluids involved in heat exchange, and on the thermal property of the conductive partition (for indirect contact heat exchangers). Materials in a heat exchanger experience stress from the temperature difference of the hot and cold fluids, and the internal pressure containing the fluids.
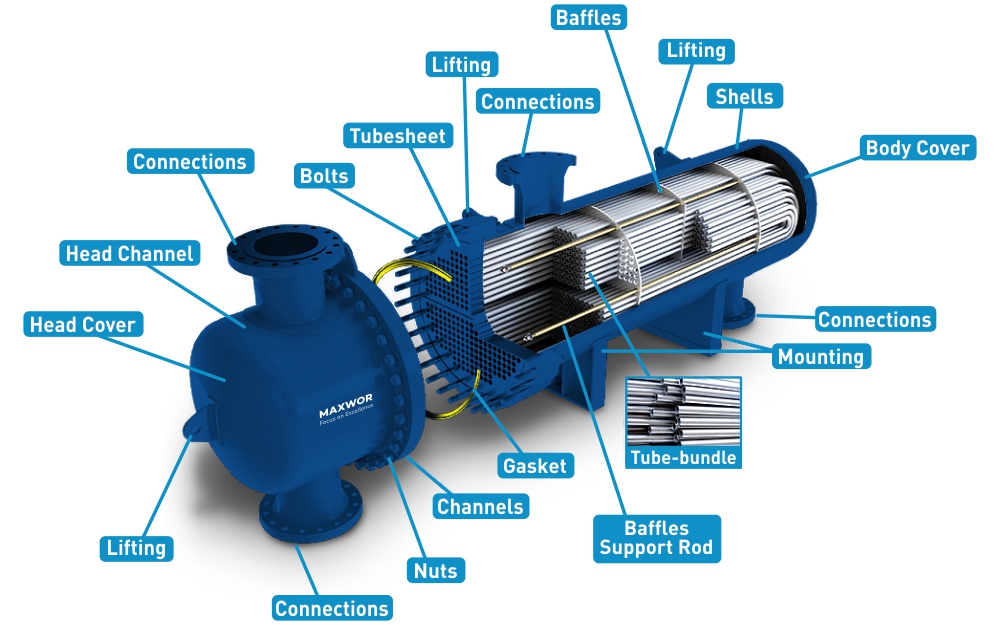
Boilers are heat transfer equipment that utilizes fuel, nuclear or electrical power as sources of heat. They are typically composed of an enclosed vessel that allows heat transfer from the source to the fluid. They are primarily used to heat liquids. Oftentimes, phase transformation of the fluid from liquid to vapor phase occurs inside the boiler. The vapor generated by the boiler is used for various heating applications and in power generation. Steam boilers generate steam at an elevated pressure to accelerate the blades of the turbine. Hence, the boiler vessel must have high strength to endure such high pressures and thermal stress. For the majority of materials, strength decreases with increasing temperature.
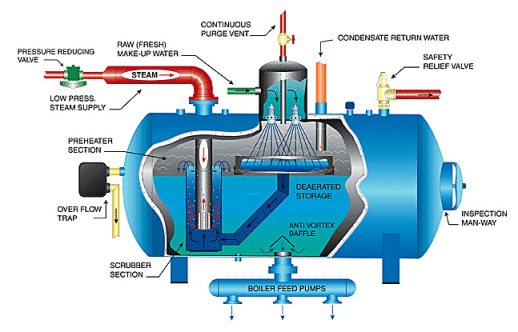
Manufacturing steps of Pressure Vessel :
1.Plate inspection
2.Plate Cutting
3.Rolling Process
4.Roll Welding
5.Barrel Formation
6.Dishend Fitting
7.Nozzel & Saddle Fitting
8.Hydrotest
9.Blasting & Painting
1.Plate Inspection
- During inspection of plate, the project code, equipment tag no., material of plate, thickness of
plate, heat number, etc. are checked and if found correct as per the requirement then marking of the shape that has to be cut from the plate is done.
- Plate inspection is done in order to ensure that the plate that came from store is exactly same
as per the desired requirement. Marking of project code, equipment tag no., material of plate,
thickness of plate etc. helps in identifying the equipment during production.
- HT is abbreviation for Heat Number. A heat number is a unique identifying code a technician
stamps on a piece of metal to provide information about its origins.
- The heat number provides a method for tracing materials and is an important part of quality
assurance and control.
- There are three segments in a heat number. The first digit indicates which furnace a
technician used to prepare a batch of molten metal. The next digits indicate the year of
casting, and the last two, three or sometimes four digits describe the number of the casting.
- As shown in photo, HT-22101943 indicate that the metal came from furnace two in the year
2021 and it was the 1943th melt for that furnace that year.
2.Plate Cutting
- After inspection and marking, plate is sent to the CNC Plasma-cutting
machine for cutting process.
- The marked dimensions are programmed by the machine operator and then the cutting
operation begins.
- As nitrogen gas is very expensive, argon and hydrogen mixture are mixed with nitrogen gas
to reduce cost of cutting.
3.Rolling Process
- After the plate cutting operation is completed, the
plate is then sent to the high thick roller machine for rolling operation.
- The plate rolling machine is a type of metal forming machine which utilizes work rollers
to produce sheet metal round processing and forming.
- The plate rolling machine is also known by plate bending roller. This machine is a type of
machine tool which is employed for creating continuous point metal sheet bending.
- The plate rolling machine holds special importance in the sheet metal industry. This piece
of machinery can be used to produce cylindrical parts, conical parts, and other parts
having different arc shapes.
- The process of plate rollers is carried out by means of machines known as plate rollers,
which basically consist of three parallel steel rollers, arranged similar to the vertices of an
isosceles triangle.
- The sheet metal when passes between the lower and upper rollers change its shape and
undergo a curvature, known as the radius of curvature. This so-called radius depends on
the mutual position of the three steel rollers.
4.Roll Welding
- Welding of rolled
shell is carried out in longitudinal direction by using SAW machine.
- Longitudinal welding is a special type of welding technique used in shell production
applications wherein the finished products need an exceptionally high wall thickness because
of the high internal or external pressures.
- The shells which were temporarily joined together by TIG welding are permanently joined
together by Submerged Arc Welding.
- Initially the ends of plate where the welding is going to be done is checked by DPT for
surface defects.
- Then welding edge preparation is carried out and the defect if found in DPT is removed with
the help of grinding.
- After welding edge preparation is completed, the shell is welded from outside by using weld
column and boom SAW machine.
5.Barrel Formation
- This vessel body or say barrel is fabricated by Circumferential SAW welding of 2 or more than 2
shells
- A circumferential weld is a type of weld that is used to join two round objects around
their circumference.
- In this way 10 shells are joined together one by one around their circumference and one
barrel is produced.
- Initially the setup for CS welding is done by TIG welding and root filing of 2 shells
from both inner and outer side.
- Then, the surface is checked by DPT for defects. If no defect found then surface is
cleaned and SAW welding on outer side is done by using Weld Column and Boom
Machine.
6.Dishend Fitting
- Dished ends are the end caps welded to the main body of a pressure vessel.
- It is major Part of Pressure Vessel which closes ends of the cylindrical section or shell of the
pressure vessel is called as Pressure Vessels Heads. There are various common names are
used for Pressure Vessels Heads which are Dish Ends, Formed Heads, End Closure, End
Caps, Vessel Ends, Vessel Caps etc. but most Common name is Dish ends.
- It is major Part of Pressure Vessel which closes ends of the cylindrical section or shell of the
pressure vessel is called as Pressure Vessels Heads. There are various common names are
used for Pressure Vessels Heads which are Dish Ends, Formed Heads, End Closure, End
Caps, Vessel Ends, Vessel Caps etc. but most Common name is Dish ends.
- Here we are using Ellipsoidal Heads to cover vessel body heads.
- SAW machine with Trolley is used in welding of Dish Ends plates. First the outer side of dish
end is welded on both the segments of plate i.e., Left Hand Side Segment and Right Hand
Side Segment.
- Then this plate is turned back, grinding is done for edge preparation, surface is checked by
DPT, and then Submerged arc welding is carried out on both the segments.
7.Nozzel & Saddle Fitting
- Draftsman explains and guides the worker to mark accessory on required location and
dimension as per the General Arrangement Drawing.
- Initially marking is done by chalk and then the marked area is manually punched by Dot
Punch and hammer.
- After punching is completed, it is checked by Production Supervisor and then it is passed for
Air Plasma Cutting operation.
- Compressed air is the most versatile of all plasma gases common for low cutting, which
produces top-quality cuts on mild and stainless steel.
Compressed air proves to be an economical choice since air is freely available. We only need
a separate air compressor to run this setup, or, a plasma cutter with on built-in.
- This machine is specially designed for heavy duty cycle to suit shop floor atmosphere. An
internal protection cut the arc in case of insufficient air pressure for the safety of the machine
as well as the operator.
- The plates for manufacturing the saddles are being cut in
CNC plasma cutting machine.
- After cutting, the plates are sent in SMAW section, where initially saddle setup is carried out
by welding stacks to temporarily join plates.
- The parallelism of plates is checked and then Shielded Metal Arc welding is done on both
the sides of plates.
- In this way Bottom and top saddles are prepared.
After preparing both the parts of saddle, these parts are welded together in order to make one
saddle support.
- In this way, Fixed and Sliding saddles are fabricated.
8.Hydrotest
- Hydro testing, more formally called
hydrostatic testing, is a type of test that is performed on pressure vessels to check for leaks.
- Hydro testing involves completely filling up a pressure vessel with water and then
pressurizing it. Once pressurized, leaks can be detected.
- Hydro testing can be used to determine if a pressure vessel has the correct mechanical
properties.
- Hydro testing is useful because the test itself uses a pressurized liquid to determine whether a
leak is present, somewhat replicating what the pressure vessel will actually go through during
its service life.
- Hydrostatic pressure is set by using following equation,
Hydrostatic Pressure = 1.3 x Maximum Allowable Working Pressure
9.Blasting & Painting
- Traditional wet
painting involves a solvent-based or water-based paint being sprayed onto a surface. The blast and
paint technique are more intensive and can be broken down into 3 steps:
pretreatment, application, and curing.
- Blasting involves propelling a stream of abrasive material against a surface under high
pressure.
- It is a fast and economical process for smoothing a rough surface, roughening a smooth
surface, shaping a surface, removing existing coatings, and cleaning off contaminants such as
rust and scale.
- The etching and scratching in the surface prepare the surface so that the paint bonds and
sticks with it. Without this step, paint chips more easily.
- Sandblasting strips the oxidation off of the steel. Leaving it exposed and not properly
finished in the wrong environment will cause rust to form quickly.
- The part is allowed to dry in a safe atmosphere before the next step.
- After pretreatment, a zinc-based primer and the powder are electrically applied with a
electrostatic gun (reminiscent of a hairdryer).
- The electrostatic gun aids in the even distribution and speed of the application.
- This also has the double benefit of preventing over-spraying since excess paint is repelled.
- Finally, the part is taken to a furnace where it is cured and the primer gels. After the primer
has been heated and gelled the final coat is applied.
- Finally, the part is taken to a furnace where it is cured and the primer gels. After the primer
has been heated and gelled the final coat is applied.
- Reduced costs, resistance and smooth finishes are the advantages of powder coating,
advantages that wet paint can't match.